Custom Tooling Manufacturing Using Advanced EDM Technology in Wisconsin
Sinker EDM is an essential machining process for any Wisconsin business built on precision. Using an electrode submerged in an insulating fluid, we can remove minute amounts of material to the tightest specifications. Our sinker EDM machines give us the machining capability to create parts unachievable with conventional cutting processes.
Contact us to get access to our Wisconsin sinker EDM capabilities on your project.
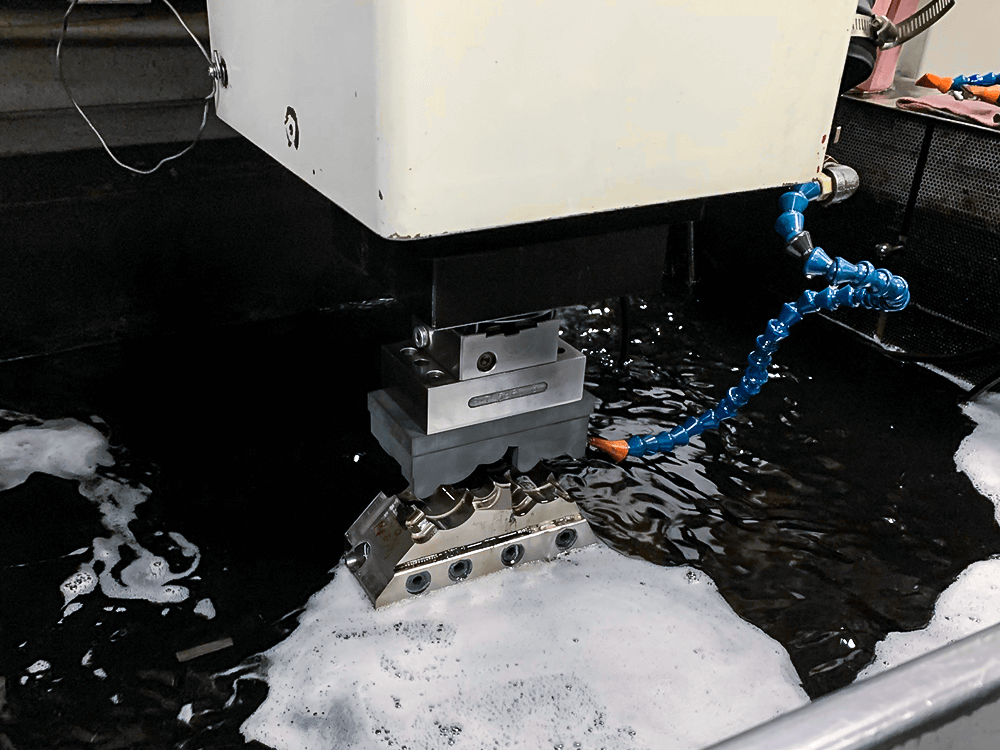
Sinker EDM for Custom Mold Making
CDM Tool's sinker EDM capabilities contribute to our precision mold making abilities. Sinker EDM enables us to create intricate mold cavities, fine details and sharp corners with exceptional accuracy. By integrating EDM into our workflow, we deliver complex geometries that traditional machining cannot achieve, ensuring your injection molds maintain performance over time.
Our Sinker EDM Capabilities
Sinker EDM lends the ability to burn deep & thin areas often impossible with traditional machining. Our Ingersoll Gantry 1300 has a 4’ x 8’ table, one of few in the United States.
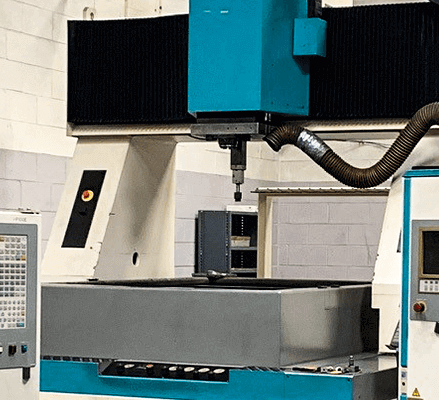
Ingersoll Gantry 1300
-
Max. Submersion: 28.5"
-
Max. Electrode Weight: 1500 lbs
-
RA MicroInch Finish: 63
-
Tank Size: 51 x 87 x36 inch
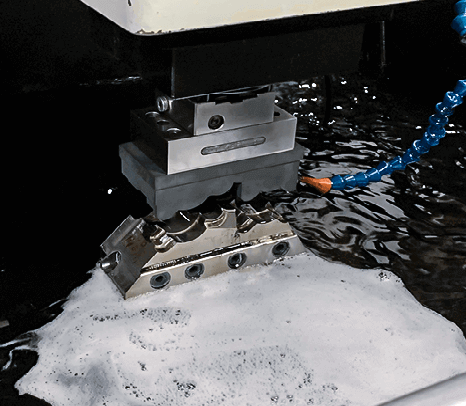
Mitsubishi EX30 (QTY 2)
-
Max. Submersion: 16.5"
-
Max. Electrode Weight: 8 lbs
-
RA MicroInch Finish: 32
-
Tool Changes: 8 and 24 Count
-
Tank Size: 27 x 19 x 13 inch
CDM Tool & Mfg provides custom tooling manufacturing using advanced EDM technology in Wisconsin, Illinois, Michigan, Minnesota, Iowa, Missouri, Ohio, Indiana, North Carolina, South Carolina, Alabama, Georgia, Kentucky, and more. Get an estimate.
Frequently Asked Questions
What is a sinker EDM machine?
Sinker EDM machines use an electrode submerged within an insulating fluid, such as oil or dielectric water, to remove minute amounts of material from a workpiece. Commonly used in the tooling and mold-making process, Sinker EDM machines are an important tool in the precision shaping process.
What are the advantages of EDM?
EDM, known as electrical discharge machining, is a non-traditional option for cutting and shaping material where traditional machining methods fall short. Advantages of EDM include the precise cutting of internal corners, the ability to shape thin walls, slots and other special part characteristics and cost savings from the lack of required special tooling.
Is EDM the same as CNC?
While EDM and CNC machines feature similar construction and tooling capabilities, EDM uses electrical discharges or sparks to cut through metal instead of the sharp cutting tools CNC machines use.